Turnaround
Turnaround in refinery service
A turnaround is a planned shutdown or interruption of normal operations at a refinery or other industrial facility. This shutdown can last weeks to months and is used to perform routine maintenance, repairs, inspections, and upgrades to the equipment During the turnaround, large portions of the plant are typically shut down, up to and including the entire plant shutdown, to ensure that the work can be performed safely and efficiently. This is critical to ensure the safety, efficiency, and long-term reliability of the plant.
Continuously trained technicians
Project engineers for planning and logistics
Days a year since 1994
neutral assembly vehicles
Key Steps and Processes Performed During a Turnaround
1. Planning and Preparation
The turnaround process typically begins in advance with a thorough planning phase. During this phase, work, resources, and schedules are carefully defined. A detailed turnaround plan is created, including all required steps and tasks This includes identifying and coordinating the system components to be maintained and determining the types of work that need to be carried out.
2. Announcement of the Turnaround
Announcement of the turnaround is made early to prepare the plant for the upcoming shutdown. Employees and contractors are informed, and safety precautions are reinforced.
3. Decommissioning the Facility
This is a critical step in which the plant is shut down in stages to ensure that it is safely accessible for the work ahead. The decomissioning follows a precise schedule and requires careful coordination.
4. Inspection and Maintenance
Extensive inspection and maintenance are performed during the turnaround. This includes checking plant components for wear, damage, or corrosion Repairs and parts replacement are executed to maintain optimal performance.
5. Modernization and Improvements
Upgrades and improvements are often made during a turnaround to increase efficiency, safety, and environmental performance. This may include installing new equipment, updating control systems, or other upgrades.
6. Testing and Commissioning
Once the work has been completed, extensive tests are carried out to ensure that the system functions properly and meets safety standards. Only after successful testing and regulatory approvals is the plant allowed to return to production.
7. Documentation and Reporting
Detailed records and reports are maintained throughout the turnaround process. This serves to document the work carried out and to analyze the results.
8. Training and Safety
Ongoing employee training and adherence to safety standards are top priorities to ensure all work is performed safely and without accidents.
Quality and safety are ingrained in us
We support you with experienced technicians who are trained in both technical and safety aspects. Our multilingual employees can provide you with the best possible international support – from supervisors, foremen, refinery fitters and pipeline constructors to safety specialists and manhole guards, we have the right personnel for you.
The most common applications in refinery service
- Column work – indoor and outdoor
- Fittings service and logistics
- Heat exchanger work
- Work on and in reactors and vessels
- Work under respiratory protection
- Bundle pulling
- Removal and installation of individual parts, seals, filters
- Installation and removal of gasketed blinds
- Parts transport
- Shutdown coordination
- Shutdown planning
Our places of operation
We assemble and service
- with continuously trained specialist fitters
- with project engineers for planning and logistics
- 365 days a year since 1994
- in clean, neutral work attire
- with neutral workshop assembly trucks (including lifting platform and crane truck)
- according to TÜV guidelines SCC** and SCP
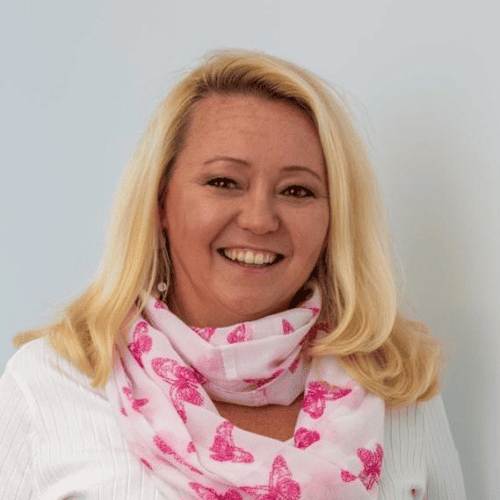
Sylvia Schütze, MAS
Commercial Management | Head of Refinery Services